Standards & Best Practices
Thermography ISO Standards
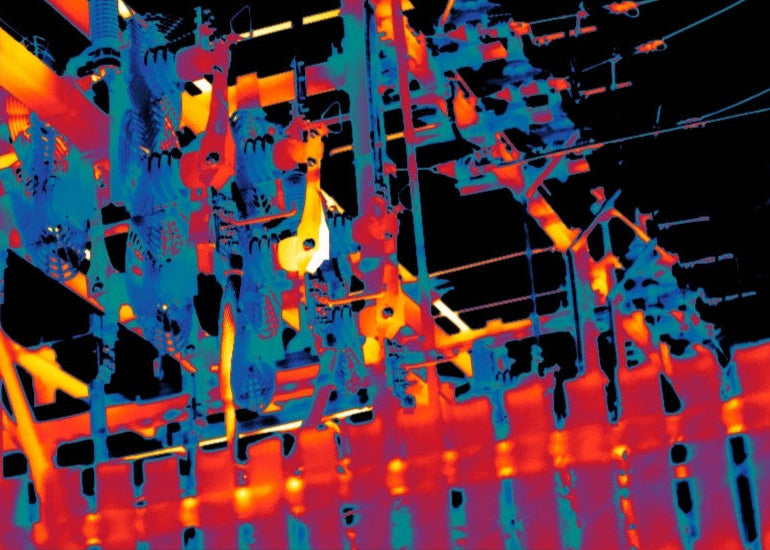
ISO 10878:2013, titled Non-destructive testing — Infrared thermography — Vocabulary
ISO 10878:2013, titled Non-destructive testing — Infrared thermography — Vocabulary, is an international standard that establishes a comprehensive set of terms and definitions used in infrared thermography for non-destructive testing (NDT). Its primary purpose is to provide a unified vocabulary to facilitate clear communication and consistency among professionals and organizations involved in NDT practices.
Infrared thermography is a technique that detects and visualizes temperature variations on the surface of objects, enabling the identification of anomalies or defects without causing damage. This standard supports the effective application of infrared thermography across various industries by ensuring that all stakeholders use consistent terminology.
ISO 10878:2013 was published in November 2013 and remains current following its last review in 2019. However, a revised edition, ISO/CD 10878, is currently under development to update and expand upon the existing terminology.
This document is available for purchase and download at: https://sabs.isolutions.iso.org/obp/ui/#iso:std:iso:10878:ed-1:v1:en:term:1.65.
ISO 18251-1:2017 – Non-destructive testing — Infrared thermography — Part 1: Characteristics of system and equipment
ISO 18251-1:2017 outlines the key components and their characteristics that constitute an infrared (IR) imaging system used in non-destructive testing (NDT). It serves as a guide for users to select appropriate IR systems tailored to specific measurement tasks. The standard details elements such as the objective lens, detector, image processor, display, thermal stimulation source, and accessories. By providing this information, it ensures that practitioners can make informed decisions when choosing equipment for effective thermographic inspections.
The primary purpose of this standard is to establish a common understanding of the components and functionalities of IR imaging systems in the context of NDT. By standardizing the descriptions and requirements of these systems, ISO 18251-1:2017 facilitates consistency and reliability in thermographic testing practices across various industries. This contributes to improved safety, quality assurance, and maintenance procedures by enabling accurate detection of anomalies through thermal imaging.
This document is available for purchase and download at: https://sabs.isolutions.iso.org/obp/ui/#iso:std:iso:18251:-1:ed-1:v1:en
ISO 18251-2:2023 – Non-destructive testing — Infrared thermography — Part 2: Test method for integrated performance of system and equipment
ISO 18251-2:2023 provides standardized test methods to evaluate the integrated performance of infrared thermography systems used in non-destructive testing (NDT). It outlines procedures to assess the combined functionality of system components, including thermal imaging devices, optics, and related equipment, ensuring they operate cohesively to deliver accurate and reliable thermal measurements.
The primary purpose of this standard is to establish consistent testing protocols for verifying the overall performance of infrared thermography systems in NDT applications. By doing so, it ensures that these systems meet the necessary quality and reliability standards, facilitating effective detection of anomalies and contributing to the safety and maintenance of various industrial assets.
This document is available for purchase and download at: https://sabs.isolutions.iso.org/obp/ui/#iso:std:iso:18251:-2:ed-1:v1:en
ISO 18434-1:2008 – Condition Monitoring and Diagnostics of Machines — Thermography — Part 1: General Procedures
ISO 18434-1:2008 provides general procedures for the application of infrared thermography in the condition monitoring and diagnostics of machines. It outlines standardized methods for using thermal imaging to detect and assess anomalies in machinery, contributing to predictive maintenance and reliability management.
The primary purpose of this standard is to establish consistent procedures for conducting thermographic inspections, ensuring accurate and reliable detection of thermal anomalies. This aids in identifying potential issues before they lead to equipment failure, thereby enhancing maintenance strategies and operational efficiency.
This document is available for purchase and download at: https://sabs.isolutions.iso.org/obp/ui/#iso:std:iso:18434:-1:ed-1:v1:en
ISO 18434-2:2019 – Condition Monitoring and Diagnostics of Machine Systems — Thermography — Part 2: Image Interpretation and Diagnostics
ISO 18434-2:2019 provides specific guidance on the interpretation of infrared thermograms as part of a program for condition monitoring and diagnostics of machine systems. It outlines methods and requirements for conducting thermographic inspections, including safety recommendations, and offers information on image interpretation, assessment criteria, and reporting requirements.
The primary purpose of this standard is to establish consistent procedures for interpreting thermal images to identify anomalies in machinery. By doing so, it aids in the early detection of potential issues, enhancing maintenance strategies and operational efficiency.
This document is available for purchase and download at: https://sabs.isolutions.iso.org/obp/ui/#iso:std:iso:18434:-2:ed-1:v1:en
ISO 18436-7:2014, titled Condition monitoring and diagnostics of machines — Requirements for qualification and assessment of personnel — Part 7: Thermography
ISO 18436-7:2014, titled Condition monitoring and diagnostics of machines — Requirements for qualification and assessment of personnel — Part 7: Thermography, establishes the criteria for qualifying and assessing individuals who perform machinery condition monitoring and diagnostics using infrared thermography.
The primary objective of ISO 18436-7:2014 is to ensure that personnel conducting thermographic evaluations possess the necessary theoretical knowledge and practical skills to accurately perform thermal measurements and analyses for machinery condition monitoring. This standard supports the reliability and effectiveness of predictive maintenance programs by defining competency requirements for thermography practitioners.
The standard outlines a structured classification system for thermography personnel:
Individuals qualified to perform infrared thermography following established procedures, capable of setting up equipment, collecting data, and identifying basic faults.
Personnel with advanced skills, including the ability to select appropriate thermographic techniques, analyze data, and provide detailed diagnostics.
Experts responsible for establishing thermography programs, developing procedures, and providing guidance to lower-category personnel.NSAI Standards Storei
Achieving certification or a declaration of conformity to ISO 18436-7:2014 signifies that an individual has met the defined qualifications and competencies to perform thermal measurements and analyses using portable thermal imaging equipment.
The procedures specified may not be applicable to specialized equipment or unique situations, emphasizing the need for tailored approaches in certain contexts.
This standard is part of the broader ISO 18436 series, which addresses the qualification and assessment of personnel involved in various condition monitoring and diagnostic techniques.
This document is available for purchase and download at: https://sabs.isolutions.iso.org/obp/ui/#iso:std:iso:18436:-7:ed-2:v1:en
Thermography Best Practice
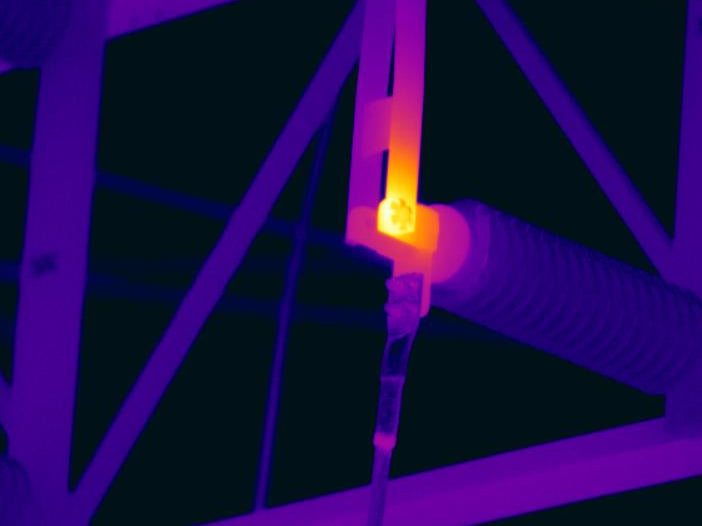
Thermographer's Code of Ethics
As a registered member of the Certified Thermographers Network – Africa (CTN-A), you hereby affirm your commitment to uphold and adhere to the Thermographer's Code of Ethics in all practices.
CTN-A Code of Ethics for Thermographers
At the Certified Thermographers Network – Africa (CTN-A), we uphold the highest standards of ethical and professional conduct in Infrared Thermography. This Code of Ethics outlines the principles and values
that guide our members in delivering reliable, respectful, and responsible
services throughout the continent.
1. Professional Integrity
Conduct all thermographic work with honesty, fairness, and transparency.
Avoid conflicts of interest and disclose any potential biases to clients and stakeholders.
2. Competence and Continuous Learning
Only undertake work for which you are qualified by education, training, and experience.
Commit to continuous professional development to stay abreast of advances in thermographic technology and best practices.
3. Confidentiality and Data Protection
Always protect client information and thermographic data.
Only disclose findings with proper authorization or when required by law.
Adhere to all relevant data protection regulations and ethical standards in handling sensitive information.
4. Accuracy and Objectivity
Ensure all reports and interpretations are accurate, evidence-based, and objective.
Avoid exaggerating or minimizing results.
Clearly communicate any limitations or uncertainties in the findings.
5. Safety and Compliance
Follow all applicable safety protocols and regulatory requirements during inspections.
Use properly calibrated equipment and standardized procedures to ensure safe and consistent operations.
6. Respect and Professionalism
Treat clients, colleagues, and the public with courtesy, respect, and professionalism.
Promote diversity and inclusion.
Avoid any form of discrimination or prejudice.
7. Environmental Responsibility
Minimize environmental impact when conducting thermographic inspections.
Support and promote practices that contribute to sustainability and environmental stewardship within the industry.
8. Accountability
Take full responsibility for your professional conduct and decisions.
Report any unethical behaviour or violations of this Code to the appropriate authorities or professional bodies.
A Commitment to Excellence
This Code of Ethics is the foundation of professional practice for all CTN-A members. By adhering to these principles, thermographers demonstrate a shared commitment to trust, integrity, and excellence in the field of infrared thermography across Africa.
The 7 Key Points to Check in Thermography for Accurate Temperature Measurement
To achieve accurate temperature readings using infrared thermography, it is essential to follow best practices across seven critical factors:
1) Focus
A properly focused image ensures precise temperature measurement. Use manual or automatic focus features to sharpen the thermal image, especially when analysing small or detailed components. An out-of-focus image can lead to temperature averaging and misinterpretation.
2) Spot Size and Target Size
Ensure that the target is significantly larger than the camera’s spot measurement area. A good rule is that the target should be at least 3 to 4 times larger than the spot size to avoid blending background temperatures into the reading.
3) Atmospheric Conditions
Factors like humidity, dust, and ambient temperature affect infrared transmission. Input atmospheric data into the thermal imager when required, and avoid glass or plastic, as these will block or distort infrared radiation.
4) Distance to Target
The further you are from a target; the more atmospheric interference and measurement error can occur. Always stay within the recommended distance for the camera’s resolution (spatial resolution or D:S ratio), ensuring sufficient detectors cover the target for clear analysis.
5) Reflected Apparent Temperature
Reflected infrared radiation from nearby surfaces can affect the accuracy of temperature readings. Use the reflector or direct method as outlined in ISO 18434 to determine the reflected temperature and enter this value into the thermal imager's settings for compensation.
6) Emissivity
Emissivity is the efficiency with which a surface emits infrared radiation. Always adjust the emissivity setting on the thermal imager to match the target material. High-emissivity materials like painted surfaces or electrical insulation provide more accurate readings than shiny metals.
For reflective surfaces, apply emissivity enhancing coatings such as electrical tape or paint to improve accuracy.
7) Viewing Angle
Aim to capture thermal images perpendicular (as close to 90° as possible) to the surface. Tilted angles influence reflection and reduce measurement accuracy. If perpendicular access is not possible, correct for angle-related emissivity changes.
By consistently applying these best practices, thermographers can ensure reliable, repeatable, and accurate temperature measurements in machinery condition monitoring and diagnostics.
Determining Emissivity Using the Reference Method (ISO 18434)
Accurate emissivity determination is critical in thermography, as it directly influences temperature measurement accuracy. The reference method, as described in ISO 18434, is one of the most reliable techniques for establishing a material's emissivity under actual operating conditions. This method involves comparing the infrared measurement of a surface to a known temperature reference.
Step-by-Step Procedure:
Identify a SAFE and Stable Test Area
Select a portion of the material’s surface that is clean, flat, and representative of the overall target. The surface should be at a stable operating temperature to ensure consistent readings.
Measure Actual Surface Temperature
Attach a high-emissivity reference such as electrical tape (typically with an emissivity of 0.95) or a painted dot to the selected area. Allow it to reach thermal equilibrium with the surface. Then use the thermal imager to measure the temperature of this reference spot.
Adjust Emissivity on Thermal Imager
Without changing the viewing angle, distance, or focus, measure the temperature of the bare material adjacent to the reference spot. Adjust the emissivity setting on the thermal imager until the measured temperature of the bare surface matches the temperature of the high-emissivity reference. The adjusted value is the estimated emissivity of the material.
Verify and Record
Repeat the procedure at multiple locations (if practical) to confirm consistency. Document the emissivity value, environmental conditions, and surface characteristics for traceability and future reference.
Key Considerations:
Safety First: Ensure the work area is safe before beginning any measurements. Do not approach or touch equipment if there is a risk of electrical shock or exposure to excessive heat that could cause injury. All potential safety hazards must be identified and addressed to maintain a safe working environment.
Surface Preparation: Ensure the material surface is clean and free of oxidation, oil, or coatings that could alter emissivity.
Environmental Control: Conduct the test in stable ambient conditions to avoid interference from wind, moisture, or fluctuating background temperatures.
Viewing Angle: Always perform the comparison from a perpendicular or near-perpendicular angle to minimize reflection and distortion.
Avoid External Heat Sources: Ensure no other hot objects are reflecting onto the target area during measurement.
Advantages of the Reference Method:
Provides a practical and relatively simple way to determine emissivity without needing detailed surface composition data.
Ensures that temperature readings during subsequent inspections are based on realistic emissivity settings for that specific material and surface condition.
By applying the reference method carefully, thermographers can greatly improve the accuracy of thermal measurements, which is essential for effective condition monitoring, diagnostics, and predictive maintenance.
Determining Emissivity Using the Contact Method (ISO 18434)
Determining the emissivity of a material is essential for accurate temperature measurement in thermography. The contact method, as outlined in ISO 18434, involves using a direct-contact temperature sensor to compare with infrared readings, allowing for a more precise emissivity setting. This method is particularly useful when non-contact methods are impractical or when high measurement accuracy is required.
Step-by-Step Procedure:
Before starting, confirm that the area is safe. De-energize equipment if possible, especially when working near live electrical components or high temperature surfaces. Wear appropriate personal protective equipment (PPE), such as insulated gloves, arc-rated clothing, and safety glasses. Never place hands or instruments on live conductors or hot surfaces without proper precautions.
Select and Prepare the Measurement Surface
Choose a clean, flat area of the material that is representative of the surface to be monitored. Remove any oxidation, dirt, or paint to expose the true surface material. Consistency in surface condition is vital for reliable results.
Attach a Contact Temperature Sensor
Use a reliable surface-contact temperature sensor (such as a thermocouple or RTD) and firmly attach it to the target area using thermal paste or high-temperature adhesive tape. Allow time for the sensor to reach thermal equilibrium with the surface. Record the temperature displayed by the sensor.
Capture the Thermal Image
With your infrared camera, focus on the same surface area where the contact sensor is attached. Ensure optimal focus, viewing angle (preferably perpendicular), and correct distance. Set the emissivity value on the imager to an initial estimate (e.g., 0.90) and observe the infrared temperature reading.
Adjust Emissivity for Accuracy
Gradually adjust the emissivity setting on the thermal imager until the displayed temperature matches the reading from the contact sensor. The emissivity value at this point is the best estimate for that material and surface condition.
Document the Results
Record the determined emissivity, the type of contact sensor used, surface condition, and environmental conditions. This information is essential for repeatability and future inspections.
Safety Hazards and Mitigation:
- Never place contact sensors on energized electrical equipment unless it is designed for live testing and you are trained and equipped for such tasks.
- Avoid contact with hot surfaces; confirm temperatures with a non-contact method first, and use high-temperature gloves when necessary.
- Watch for moving parts, pinch points, or unstable surfaces.
Conclusion:
The contact method offers high accuracy in determining emissivity, especially when surface conditions and safety allow for direct access. Following ISO 18434 and observing all safety protocols ensures reliable results and protects personnel from harm.
Determining Reflected Apparent Temperature (or T reflect) Using the Reflector Method (ISO 18434)
In thermography, accurately determining the reflected apparent temperature is essential for precise surface temperature measurements, especially for low-emissivity materials. According to ISO 18434, the reflector method is a standard and practical approach to estimating this value by simulating the infrared radiation reflected onto the target surface from surrounding objects.
Step-by-Step Procedure:
Before starting, assess all safety risks. When working near energized electrical systems or hot machinery, use appropriate PPE such as arc-rated clothing, insulated gloves, and eye protection. If possible, de-energize equipment to eliminate the risk of electric shock or burns. Be aware of hot surfaces, moving machinery, or unstable platforms.
Prepare the Reflective Material:
Obtain a piece of crumpled and flattened aluminum foil or similar highly reflective, low-emissivity material. This will act as a mirror for ambient infrared radiation. The foil should be clean and wrinkle-free enough to reflect surrounding objects clearly, but dull enough to avoid acting as a direct mirror.
Place the Reflector Near the Target Surface
Secure the foil close to the surface whose temperature you wish to measure. Ideally at the same angle and orientation. It must reflect the same environmental conditions affecting the target. Avoid letting the foil touch live components or hot surfaces. If placement near energized equipment is required, maintain safe distances or use non-conductive holders.
Set the Thermal Imager’s Emissivity to 1.0
On your infrared camera, set the emissivity to 1.0 (assuming a perfect blackbody) and distance to 0 meters to minimize atmospheric influence. This setting allows you to isolate the reflected radiation being captured by the foil.
Measure the Apparent Temperature of the Reflector
Focus the thermal imager on the foil and measure its apparent temperature. This value represents the reflected apparent temperature from the environment, which should be used in all subsequent measurements involving that surface or area.
Input the Reflected Temperature into the Thermal Imager
Update the reflected apparent temperature setting in your imager with the measured value. This will improve the accuracy of surface temperature calculations, especially for materials with low emissivity.
Key Safety Hazards and Precautions:
- Electrical Shock: Never place foil near live electrical components unless equipment is isolated or you're trained and wearing certified PPE.
- Burn Injuries: Avoid placing the reflector on or near high-temperature surfaces that could ignite materials or cause skin burns.
- Reflected Heat: Be cautious of hot equipment radiating heat back onto your face or hands while positioning the reflector.
Conclusion:
Using the reflector method per ISO 18434 is a reliable way to determine reflected apparent temperature. When done safely and accurately, it significantly enhances thermographic measurement precision in real-world industrial environments.